-
Home
-
Publications and submissions
-
Reports
-
EWON Insights
-
EWON Insights Oct-Dec 2020
- Quality assurance - our internal review process
Quality assurance - our internal review process
We have a comprehensive internal Quality Assurance Framework. Separate from our Investigations Team, our Quality Team undertakes in-depth, fair assessments of our complaint work including adherence to our complaint-handling and investigations policies and procedures. This includes being accountable, transparent, timely and fair.
When a customer asks for a review of their case, it give us an opportunity to identify potential improvements in our decision-making processes. It also gives us a chance to reconsider the complaint in light of further information or an alternative interpretation of available information.
While most internal reviews find that the review grounds are not upheld, in this case study the information provided by the customer substantiated one or more of the grounds for review.
Case studies
Customers claim for compensation accepted after EWON review
A customer told EWON that a distributor’s tree trimming sub-contractor attended her rural property to complete vegetation management works. She and two others witnessed the sub-contractor’s truck stop outside her house to trim trees before driving up a narrow driveway to the top of the hill to be able to turn around and leave.
Shortly after she noticed a private pole on the property was leaning, so engaged an electrician to inspect the pole which was initially identified as sagging due to rotting underground. On replacement, it was then identified as being structurally sound. Her electrician advised her that the damage to the pole appeared consistent with something snagging the wire connecting it to the high voltage pole. The customer considered the tree trimmer's truck snagged the wire as no other vehicle of sufficient height had been on the property. On this basis she made a claim to the distributor for the pole replacement costs of $3,336, however the claim was denied.
The distributor noted that GPS tracking only showed the tree trimmer's vehicle going as far as the first building on the property, therefore it maintained the truck could not have clipped the wires. The customer noted it was physically impossible for a truck to turn around at the point where the GPS records showed. She also noted GPS devices have a start-up lag time and a truck could drive up the hill and loop back down without the GPS showing this.
Our original investigation concluded that, while it could not be ruled out the tree trimmer's truck had driven up the hill and clipped the wires, there was insufficient supporting information to substantiate this and so the denial of the claim was upheld. The customer then requested a review.
Our Internal Review noted the photography of the terrain appeared to support the customer's statement that it was impossible for a truck to turn around where the GPS records indicated. Also, a review of GPS device information supported the customer's advice that GPS devices could have a start up lag of up to five minutes while it searched for satellite signals. This supported the idea that a truck could drive up the hill and loop around before a signal was established.
The important question was how a standard-sized truck could have clipped the wire if it had adequate clearance from the ground. The high voltage wire to the private pole was noted as being the distributor’s responsibility to maintain. This issue had not been identified in our investigation and feedback was provided to the Investigations Team. The pole maintenance records on the property indicated numerous reported defects about the clearance height of high and low voltage wires. A work order on the distributor’s database to rectify the issue appeared to be open since it was initially reported in 2016. This additional relevant information formed the basis for upholding the grounds for review.
Following our advice that this information and the questions around the wire clearance defects merited further investigation, the distributor agreed to pay the customer's claim of $3,336.
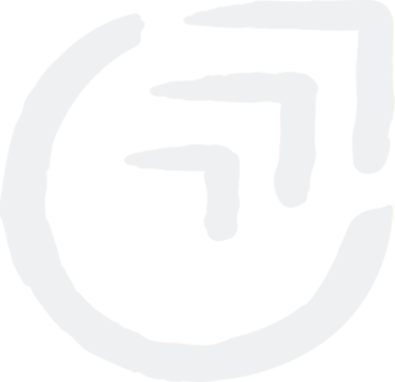